The Comprehensive Guide to Concrete Batching Plants
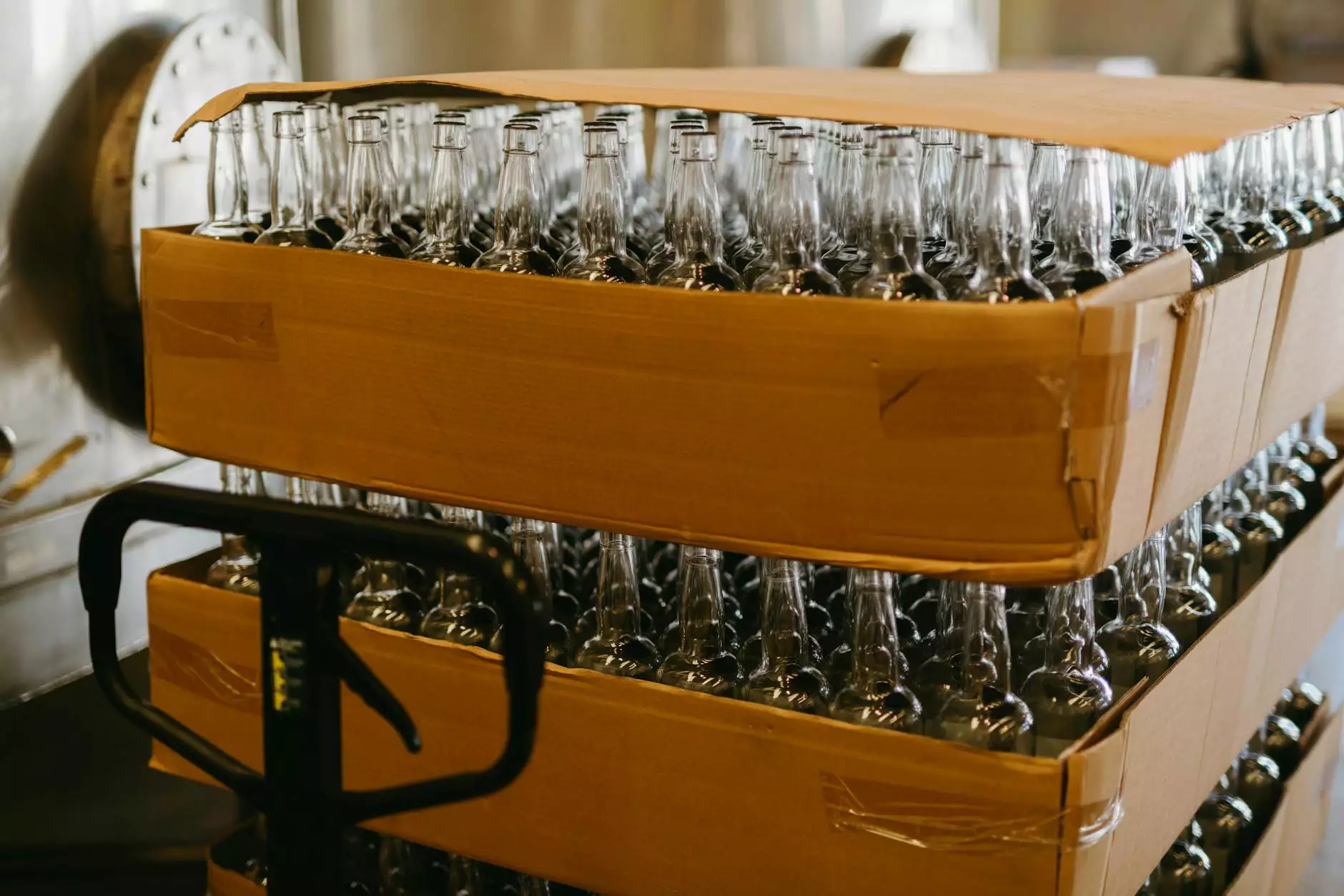
Concrete batching plants are essential components in the construction industry, playing a pivotal role in producing concrete for various projects. This article delves into the functions, types, and benefits of these plants, providing a well-rounded understanding of their significance in modern construction.
What is a Concrete Batching Plant?
A concrete batching plant is a facility that combines various ingredients to form concrete. The primary materials used in this process include:
- Cement
- Water
- Aggregates (sand, gravel, or crushed stone)
- Additives and admixtures
These components are accurately measured and mixed in prescribed proportions to create a homogeneous and high-quality concrete mix, which is essential for construction projects of all sizes.
The Importance of Concrete Batching Plants in Construction
Concrete is one of the most widely used construction materials due to its durability, flexibility, and strength. The significance of concrete batching plants can be observed in the following aspects:
- Efficiency: Automated processes in batching plants ensure rapid production cycles, enabling construction companies to meet tight deadlines.
- Quality Control: Modern batching plants utilize advanced technology allowing for precise measurement and mixing, resulting in high-quality concrete.
- Customization: Plants can easily adjust formulations for different types of concrete, fostering the ability to cater to specific project requirements.
- Cost-Effectiveness: The in-house production reduces transportation costs and material waste, leading to significant overall savings on any project.
Types of Concrete Batching Plants
Concrete batching plants can be categorized into two primary types:
1. Stationary Concrete Batching Plants
These plants are permanently installed at a specific site and are designed for high production rates. They consist of larger equipment and are capable of handling vast quantities of concrete. The primary features include:
- Stable foundation allowing for extensive use over long periods.
- Equipped for high-capacity output.
- Ideal for large-scale and ongoing projects.
2. Mobile Concrete Batching Plants
As the name suggests, these plants can be easily transported to various sites, providing flexibility for construction companies. Key attributes include:
- Quick setup and takedown, making them perfect for temporary projects.
- Compact design allowing for easier transportation.
- Capability of producing concrete on-site, thus reducing delivery time and costs.
Components of a Concrete Batching Plant
Understanding the different components of a concrete batching plant helps recognize its efficiency and functionality. The main parts include:
1. Aggregate Bins
These bins store various aggregates needed for concrete production. They are typically equipped with individual weigh scales to ensure accurate measurements.
2. Mixing Unit
The mixing unit is where all ingredients are combined. There are different mixing technologies, such as:
- Twin-Shaft Mixers
- Planetary Mixers
- Drum Mixers
3. Cement Silos
Cement is stored in silos until needed. They are usually designed to maintain the material's quality and are fitted with level indicators.
4. Control System
An essential part of modern batching plants, the control system oversees the entire process, allowing operators to manage production efficiently. Advanced systems may integrate computer software for better control and analytics.
How Concrete Batching Plants Work
The operation of a concrete batching plant follows a systematic process:
- Material Acquisition: Raw materials are sourced and transported to the plant.
- Weighing: Each material is accurately weighed according to the predefined recipe.
- Mixing: The weighed materials are then transferred to the mixer where they are blended thoroughly.
- Discharging: The mixed concrete is either loaded into mixer trucks for transportation or directly delivered to the construction site.
Advantages of Using a Concrete Batching Plant
Adopting a concrete batching plant has numerous advantages, including:
- Consistency: The plant ensures consistency in the quality of concrete produced.
- Sustainability: Batching plants can incorporate recycled materials, promoting sustainable construction practices.
- Reduced Labor Costs: Automation in the batching process reduces the need for extensive labor, thus lowering operational costs.
- Improved Safety: With automated processes, the risks associated with manual mixing and handling are minimized.
Key Considerations When Choosing a Concrete Batching Plant
When selecting a concrete batching plant, several factors must be considered to ensure optimal performance:
- Production Capacity: Assess the expected volume of concrete required for your projects to select an appropriately sized plant.
- Types of Concrete: Determine if the plant can produce the specific types of concrete needed.
- Site Conditions: Consider site accessibility and environmental conditions which may affect the plant’s operation.
- Budget: Evaluate both initial investment and ongoing operational costs.
Conclusion
In summary, concrete batching plants are an indispensable asset in the construction industry, enabling businesses to produce high-quality concrete efficiently and cost-effectively. Understanding their functions, advantages, and operational mechanisms can significantly enhance decision-making in construction projects. As the demand for concrete continues to grow, leveraging advanced batching technologies will provide companies with a competitive edge.
For more information about state-of-the-art concrete batching plants and related technologies, visit polygonmach.com.